Valve Trim Guide: Materials, Selection & API Standards
What is Valve Trim?
Valve trim is the collective term for the internal parts of the valve that can be removed and replaced and come into contact with the flow medium. These parts include valve seat(s), disc, glands, spacers, guides, bushings, and internal springs. The valve body, bonnet, packing, et cetera that also come in contact with the flow medium are not considered valve trim.
The disk-to-seat interface and the relationship between the disk position and the seat determine a valve’s trim performance. Basic motions and flow control are possible because of the trim. In designs with rotational motion trim, the flow opening changes when the disk moves close to the seat. An annular orifice appears when the disk lifts perpendicularly away from the seat in linear motion trim designs. Due to the various properties required to withstand various forces and conditions, valve trim parts can be constructed from a variety of materials. Bushings and packing glands do not experience the same forces and conditions as do the valve disc and seat(s).
API has standardized trim materials by assigning a unique number to each set of trim materials.
Primary Functions of Valve Trim
Valve trim is a critical component in control valves, responsible for regulating the flow of fluids (liquids, gases, or slurries) through a pipeline. The trim consists of the movable and stationary parts that directly interact with the flow, including the plug, seat, stem, and cage. The valve trim is essential for precise flow control, pressure management, and system efficiency. Selecting the right trim design ensures optimal valve performance, longevity, and reliability in various industrial applications.
Key Functions of Valve Trim:
1. Flow Control – The primary role of the trim is to modulate flow by adjusting the position of the plug relative to the seat. This controls the rate, pressure, and direction of the fluid passing through the valve.
2. Pressure Regulation – The trim helps manage pressure drops across the valve, ensuring stable operation and preventing damage from excessive pressure surges.
3. Sealing Performance – When the valve is closed, the trim ensures a tight seal between the plug and seat to prevent leakage.
4. Noise and Cavitation Reduction – Specialized trims (such as multi-stage or anti-cavitation trims) are designed to minimize noise, vibration, and erosion caused by high-velocity flows.
5. Durability in Harsh Conditions – The trim is often made from hardened materials (e.g., stainless steel, tungsten carbide) to withstand corrosive, abrasive, or high-temperature environments.
Given below is summary of the trim components perform these essential roles:
Function | Impact | Key Components Involved |
---|---|---|
Flow Control | Regulates flow rate, pressure, and direction | Disc, seat, plug |
Sealing | Ensures leak-tight shutoff (prevents fugitive emissions) | Seat, disc, stem seals |
Durability | Resists wear, corrosion, and erosion | Hard-faced seats, stem coatings |
Actuation | Transfers motion from actuator to closure element | Stem, bushings |
Key Components of a Valve Trim
Disc/Plug
The disc (in globe valves) or plug (in control and plug valves) is the primary throttling component that moves into or away from the seat to modulate or stop flow. Its design can vary (flat, tapered, contoured) based on the valve type and required flow characteristics. In high-performance or erosive applications, hard-facing materials like Stellite are used for durability.
Seat
The seat is the static part of the valve trim that contacts the disc or plug to form a seal when the valve is closed. It must be erosion and corrosion resistant to maintain leak-tightness over time. Soft-seated valves may use PTFE or elastomers for bubble-tight sealing, while metal-seated valves use harder alloys for high-temperature or abrasive conditions.
Stem
The stem is a precision-machined shaft that connects the actuator or handwheel to the disc/plug. It converts rotary or linear motion to operate the valve. The stem must withstand bending, tensile, and torsional stresses, and its surface must be resistant to galling and corrosion. Special alloys are chosen when dealing with aggressive fluids (e.g., sour service or seawater).
Bushings
Bushings (or stem guides) are sleeve-like components that support the stem and reduce metal-to-metal contact, thereby lowering friction and extending stem life. In high-cycle or high-pressure valves, low-friction materials like PTFE or graphite composites are used to ensure smooth movement and prevent galling. They also help in stem alignment and reduce side loading.
Component | Function | Common Materials |
---|---|---|
Disc/Plug | Controls flow & shutoff | Stainless steel, Stellite |
Seat | Provides sealing surface | 316SS, Tungsten Carbide |
Stem | Transfers actuator motion | 17-4PH, Monel |
Bushings | Reduces friction & wear | Bronze, PTFE |
Note: The valve body and bonnet are not considered trim, even if they contact the medium.
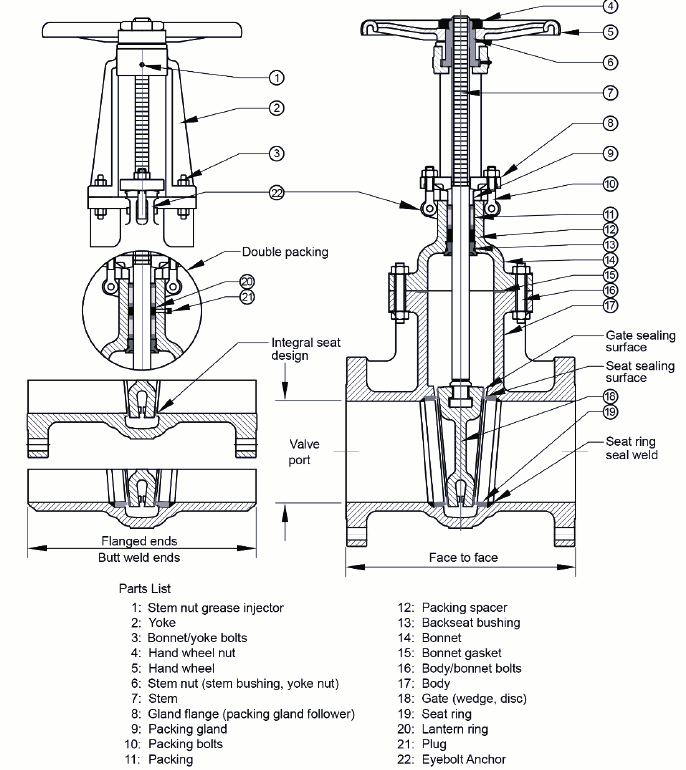
Valve Trim Materials: How to Choose the Right One
Understanding the material selection process is critical to engineering any application and/or part design. The choice of materials is the foundation upon which all valve applications are built. The most economical trim material is stainless steel. Available in different grades, this material provides strong resistance to erosive, corrosive, and temperature impacts and provides an excellent all-around choice.
In addition to stainless steel, more expensive materials such as Monel, Alloy 20, and Cu-Ni may be selected. These materials, sometimes referred to as exotic materials, generally are more expensive and have longer lead times than stainless.
Trim selection guidelines from manufacturers should be followed. One must consider trade-offs between the initial cost and the estimated service life. Stellite trim, for instance, may not be the best option if it doubles the price while extending the valve’s service life by 20%. It is essential to consider uptime, labor costs, and dependability. Engineers working on applications shouldn’t try to link operating pressures to expected wear.
Hardened Trim
Most high-pressure applications are suitable for hardened trim. Although solid hard plugs are more cost-effective for valves under 1 inch in diameter, a hard material overlay is more cost-effective for larger sizes. For services like superheated steam, two-phase flow, and temperatures above 600°F (315°C), these overlays are effective.
Why Valve Trim Selection is Critical?
1. Material Compatibility
Chemical Resistance:
- Stainless steel (Trim 8) resists chlorides and acids.
- Nickel alloys (Trim 19B) handle sulfuric/hydrochloric acid.
Temperature Limits:
- Carbon steel (Trim 1) fails above 425°C (800°F).
- 9Cr-1Mo (Trim 5) works up to 650°C (1,200°F).
2. Pressure & Erosion Resistance
- High-Pressure Services: Hardened trim (Stellite 6, 350+ HB) prevents deformation.
- Slurry/Erosive Flow: Tungsten carbide or ceramic coatings extend service life.
3. Leakage Prevention (API 598 Standards)
API 598 Standards classify leakage rates, from Class IV (0.1% leakage) to Class VI (bubble-tight). Achieving Class VI requires precision-machined metal seats or elastomers. Selecting trim to match these standards prevents costly leaks and ensures safety in harsh conditions.
Leakage Class | Allowed Leakage | Trim Requirement |
---|---|---|
Class IV | 0.1% of rated capacity | Standard soft seats |
Class VI | Zero bubbles/min (bubble-tight) | Metal-seated with lapped surfaces |
Consequences of Incorrect Trim Selection
Choosing the wrong valve trim can lead to costly failures, including premature wear, leaks, and safety risks. Soft trim in abrasive service causes seat erosion, leading to leakage and frequent maintenance. Incompatible materials in corrosive environments trigger rapid corrosion, risking valve rupture. High-temperature applications with mismatched trim suffer thermal fatigue, causing cracks. Stem galling from poor bushing selection can seize the valve, halting operations. Non-compliant trim in sour service (H₂S) may violate NACE standards, resulting in fines. Ultimately, incorrect trim increases downtime, repair costs, and operational hazards. Always match trim to fluid, pressure, and temperature conditions.
Failure Mode | Cause | Result |
---|---|---|
Seat Erosion | Soft trim in abrasive service | Leakage, frequent maintenance |
Stem Galling | Incompatible stem/bushing materials | Valve seizure |
Corrosion Failure | Wrong alloy for chemical exposure | Catastrophic rupture |
Thermal Fatigue | Mismatched expansion rates | Cracking at high temps |
Valve Trim in Different Valve Types
Valve Type | Critical Trim Components | Common Materials |
---|---|---|
Gate Valve | Seat, gate, stem | 13Cr, Stellite, Alloy 20 |
Globe Valve | Plug, seat ring, stem | SS316, Monel, Hastelloy |
Ball Valve | Ball, seats, stem | PTFE, PEEK, 17-4PH SS |
Check Valve | Disc, hinge pin, seat | 410 SS, Alloy 625 |
How to Select the Right Trim?
Follow this 4-step process:
- Identify Service Conditions: Fluid type, temperature, pressure, abrasives.
- Choose Material per Standards: API 600 (gate valves), API 602 (small valves), NACE for sour service.
- Consider Leakage Class: Metal seats for high-temp, elastomers for bubble-tight shutoff.
- Verify Compatibility: Ensure trim hardness is compatible with body materials.
API Valves Trim Table (Trim Chart)
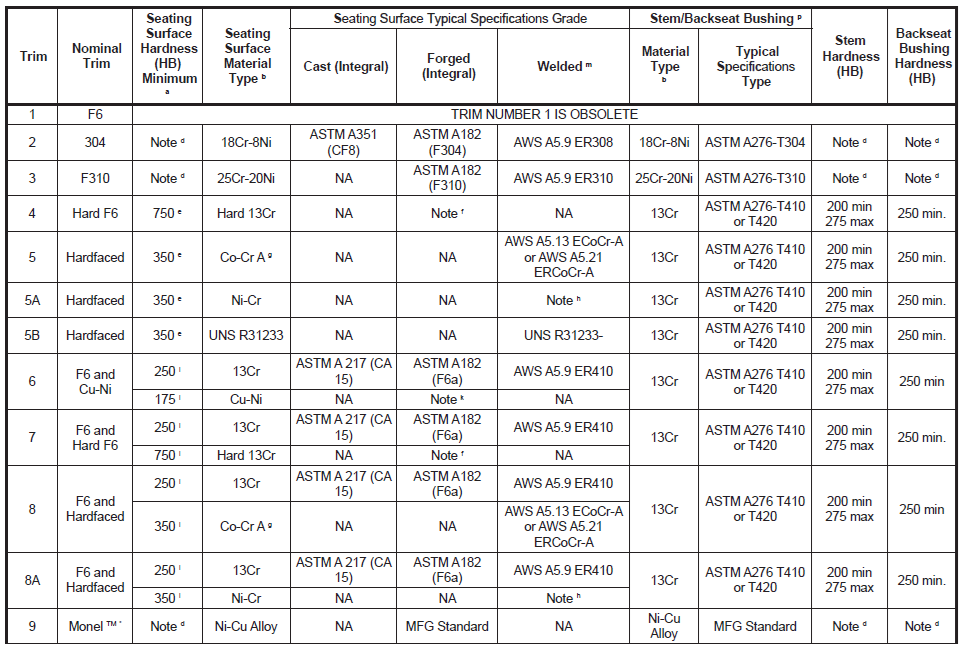
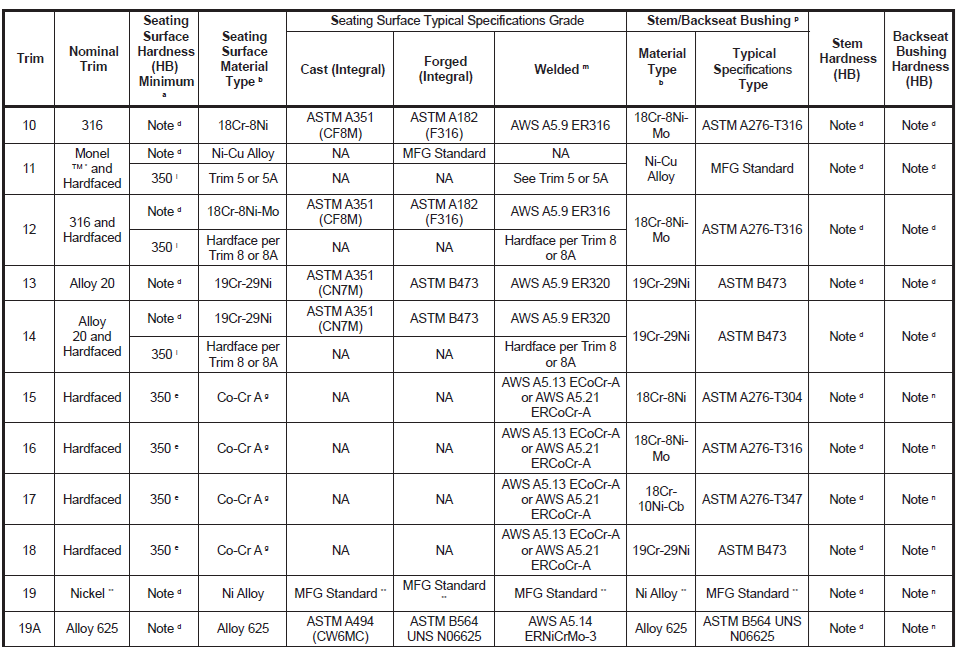
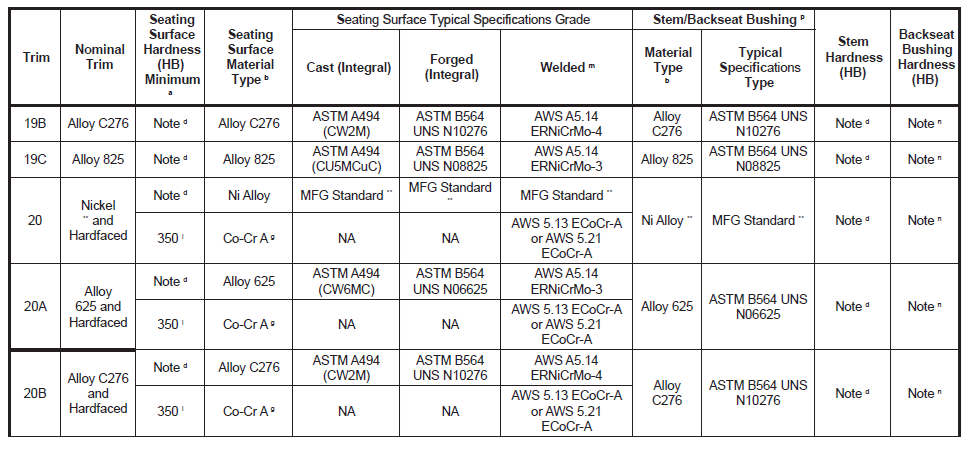
Disclaimer: Data provided about API Trim numbers is based on API Standard 600 and is for informational purposes only. Always consult current API publications to verify information and trim date. Refer API Website: https://www.api.org
Commonly Asked Questions about Valve Trim:
1. What is valve trim and why it is important?
Valve trim refers to the internal components of a valve that come into contact with the flow medium and are responsible for controlling the flow. This typically includes the disc, seat, stem, sleeves, and sometimes the bonnet. These parts determine the valve’s performance in terms of flow control, shutoff, and durability.
2. Why is valve trim material selection important and what are the common materials used for valve trim in corrosive services?
The trim material must be compatible with the process fluid to resist corrosion, erosion, and wear. Improper material selection can lead to premature failure, leakage, or operational inefficiencies. Common trim materials for corrosive services include:
- Stainless Steel (SS316, SS304) – General corrosion resistance.
- Duplex Stainless Steel (UNS S31803) – Better chloride resistance.
- Hastelloy (C276, C22) – For highly corrosive acids (HCl, H₂SO₄).
- Monel (Alloy 400/K500) – For seawater and hydrofluoric acid.
- Titanium – Excellent for chlorides and oxidizing media.
3. What is meant by ‘hard-faced’ valve trim and when would you recommend hard-faced trim (e.g., Stellite 6)
Hard-facing refers to applying a wear-resistant material (like Stellite) to the surface of trim components such as the seat and disc to increase their resistance to erosion, abrasion, or galling.
Hard-faced trim (e.g., Stellite 6, Tungsten Carbide) is recommended for:
- High-pressure, high-temperature (HPHT) services (e.g., steam, oil & gas).
- Abrasive or erosive fluids (slurries, sand-laden fluids).
- Frequent cycling applications to reduce wear.
4. What is a ‘trim number’ or ‘trim code’ and what is the difference between Trim No. 5 and Trim No. 8 in API 600?
Trim number or code is a standardized designation (e.g., as per API 600 or API 602) used to identify a specific combination of materials used for the valve’s trim components.
Trim No. 5:
- Seat/Disc: 13% Cr (410 Stainless Steel)
- Stem: 13% Cr (410 SS)
- Used for general service, moderate corrosion resistance.
Trim No. 8:
- Seat/Disc: 13% Cr (410 SS) + Stellite hard-facing.
- Stem: 13% Cr (410 SS)
- Used for erosion/cavitation resistance (e.g., steam, high-velocity flow).
5. How does valve trim affect control valve performance?
In control valves, trim design directly impacts flow characteristics, cavitation resistance, noise generation, and throttling capability. Specialized trims like cage-guided, multi-stage, or low-noise trims are engineered to manage pressure drop and prevent damage from cavitation or flashing.
6. What’s the difference between balanced and unbalanced valve trim?
Balanced trim includes features like pressure equalizing ports or double-seated designs that reduce the force needed to actuate the valve by minimizing the net force on the plug. Unbalanced trim lacks these features, requiring more actuator force and is typically used in smaller valves or less demanding services.
7. When would you recommend a high-alloy or exotic trim material?
In services with highly corrosive, erosive, or high-temperature conditions—such as seawater, acid gases, or high-pressure steam—high-alloy or exotic materials like Monel, Inconel, Hastelloy, or titanium are used to improve durability and extend the service life of the valve.
8. How can valve trim be damaged during operation?
Common causes of trim damage include cavitation, flashing, particulate erosion, corrosion, and improper actuation. Cavitation, in particular, can cause pitting and vibration, leading to leakage or structural failure of the valve.
9. What is anti-cavitation trim and when is it used?
Anti-cavitation trim is a specially designed internal valve configuration that prevents cavitation by controlling the pressure drop across the valve in multiple stages. It is used in high-pressure drop applications where cavitation could otherwise cause severe damage.
10. How does valve trim relate to Class ratings and valve standards?
The trim must withstand the pressure and temperature conditions defined by the valve’s pressure class (e.g., Class 150, 300) and should comply with applicable standards like API 600, ASME B16.34, or MSS-SP-61. The combination of body rating and trim material ensures valve integrity and safety under operating conditions.