Heat Exchanger: Working Principle, Types, Advantages, & Applications
Last Updated: 30-Jul-2025
What is a heat exchanger?
Heat exchangers are devices designed to transfer heat between two or more fluids without mixing them. They are vital in numerous industrial processes, ranging from energy systems and chemical processing to HVAC and food industries. Engineers working in process design, mechanical maintenance, or energy systems must have a solid understanding of heat exchangers to ensure optimal thermal performance and system efficiency.
Working Principle
The basic principle of a heat exchanger is based on thermal conduction and convection. A hot fluid releases heat that is transferred through a solid barrier (typically metal) to a colder fluid on the other side. Depending on the design, the fluids can be in direct or indirect contact, but most standard exchangers maintain separation.
For example, an oil cooler cools down hot oil by passing cold water next to the hot oil tube. The heat from the oil is transferred into the cold water, reducing the temperature of the oil.
Flow Arrangements
Parallel Flow: Both fluids move in the same direction. Simpler design but lower efficiency.
Counter Flow: Fluids flow in opposite directions, maximizing temperature difference and efficiency.
Cross Flow: Fluids move perpendicular to each other. Common in compact designs like air-cooled exchangers.
Types of Heat Exchangers
1. Shell and Tube Heat Exchanger
Structure: A shell and tube heat exchanger is a widely used device in industrial applications for transferring heat between two fluids. It consists of a series of tubes enclosed within a cylindrical shell, where one fluid flows through the tubes (the tube side) and the other flows outside the tubes but inside the shell (the shell side). Heat is exchanged through the tube walls, allowing efficient thermal transfer while keeping the fluids separate. These heat exchangers are highly versatile, capable of handling high pressures and temperatures, and can be designed for various configurations, such as fixed tube sheets, U-tube, or floating heads.
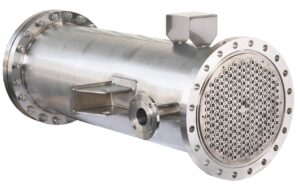
Advantages:
- Handles high pressures and temperatures.
- Easy to add multiple passes to increase efficiency.
- Modular designs can be customized.
Disadvantages:
- Large footprint and weight.
- Higher material and fabrication costs.
- Requires periodic cleaning, especially on the shell side.
Applications: Common applications include power plants, refineries, chemical processing, and HVAC systems. Their robust construction, ease of maintenance, and adaptability make them a preferred choice for many heat exchange needs.
2. Plate Heat Exchanger (PHE)
Structure: A plate heat exchanger is a compact and efficient device used to transfer heat between two fluids without mixing them. It consists of multiple thin, corrugated metal plates stacked together, forming separate channels for the hot and cold fluids. Heat is transferred through the plates as the fluids flow in alternating channels, allowing for high thermal efficiency due to the large surface area and turbulent flow. Plate heat exchangers are lightweight, easy to maintain, and can be disassembled for cleaning or expansion.
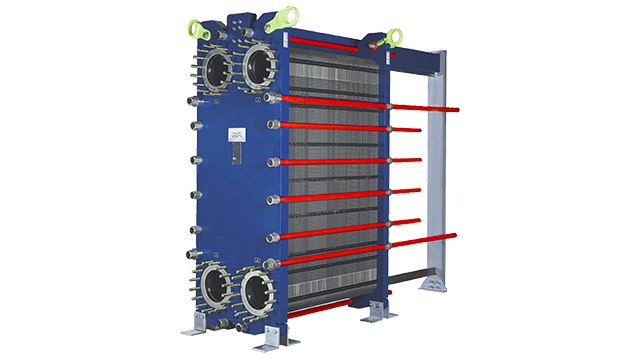
Advantages:
- Very high heat transfer coefficient due to turbulence.
- Compact and space-saving design.
- Easy to expand or service by adding/removing plates.
Disadvantages:
- Limited to relatively low pressure and temperature applications.
- Gasketed types may be prone to leakage.
- Not suitable for fluids with high fouling potential.
Applications: Plate heat exchangers are commonly used in HVAC systems, refrigeration, food processing, and chemical industries, where space-saving design and rapid heat transfer are essential. Their modular construction allows for flexibility in capacity adjustments, making them ideal for applications requiring precise temperature control.
3. Air-Cooled Heat Exchanger (ACHE)
Structure: An air-cooled heat exchanger (ACHE) is a type of heat exchanger that uses ambient air to cool or condense process fluids, eliminating the need for water as a cooling medium. It consists of finned tubes arranged in bundles, with fans forcing or drawing air across the tubes to enhance heat transfer. These exchangers are particularly useful in water-scarce areas or applications where water cooling is impractical or costly.
Advantages:
- Eliminates the need for water, reducing utility costs.
- Lower environmental impact in arid regions.
- Easy to install outdoors.
Disadvantages:
- Large physical size compared to water-cooled designs.
- Heat rejection capacity depends on ambient temperature.
- Higher fan power consumption.
Applications: ACHEs are commonly used in power plants, refineries, petrochemical facilities, and gas compression stations. They are less efficient in extremely hot climates and require larger footprints for adequate airflow. Their robust design makes them ideal for high-temperature and high-pressure applications.
4. Double Pipe Heat Exchanger
Structure: A double pipe heat exchanger, also known as a hairpin heat exchanger, is one of the simplest and most cost-effective types of heat exchangers. It consists of two concentric pipes—an inner pipe carrying one fluid and an outer pipe (shell) carrying the other. Heat is transferred through the wall of the inner pipe as the fluids flow in either parallel (co-current) or counter-current directions, with counter-flow being more efficient. Due to its straightforward design, this heat exchanger is easy to construct, maintain, and clean, making it suitable for small-scale applications, high-pressure services, or situations requiring frequent thermal cycling. However, its heat transfer area is limited compared to shell-and-tube or plate heat exchangers, making it less efficient for large-scale processes.
Advantages:
- Simple design and construction.
- Ideal for small-scale duties or high-temperature applications.
- Easy to clean and maintain.
Disadvantages:
- Not efficient for large heat duties.
- High surface area requirements.
Applications: Common uses include preheating, cooling, and heat recovery in chemical plants, food processing, and HVAC systems. Its modular design also allows for easy expansion by adding more hairpin sections in series or parallel.
Advantages of Heat Exchangers in Process Industries
1. Energy Efficiency and Cost Savings
One of the most significant advantages of heat exchangers is their ability to improve energy efficiency.
- Heat Recovery: Heat exchangers recover waste heat from exhaust gases, hot liquids, or steam, repurposing it to preheat incoming fluids. This reduces the need for additional heating, lowering fuel consumption and operational costs.
- Reduced Energy Consumption: By efficiently transferring heat between fluids, heat exchangers minimize energy losses, leading to substantial cost savings in large-scale industrial processes.
- Lower Utility Costs: Industries using heat exchangers can reduce reliance on external heating or cooling systems, decreasing electricity and fuel expenses.
2. Enhanced Process Control and Stability
Heat exchangers contribute to better process control by maintaining consistent temperatures, which is crucial for product quality and safety.
- Precise Temperature Regulation: Heat exchangers ensure that fluids reach and maintain the desired temperature, preventing overheating or undercooling in sensitive processes.
- Improved Reaction Rates: In chemical and pharmaceutical industries, maintaining optimal temperatures enhances reaction efficiency and product yield.
- Stable Operations: By preventing thermal fluctuations, heat exchangers help avoid equipment stress and process disruptions.
3. Environmental Benefits
Heat exchangers support sustainable industrial practices by reducing emissions and energy waste.
- Lower Carbon Footprint: Reusing waste heat decreases the demand for fossil fuels, reducing greenhouse gas emissions.
- Compliance with Regulations: Many industries must adhere to environmental standards, and heat exchangers help meet energy efficiency and emission control requirements.
- Reduced Water Usage: In cooling applications, heat exchangers can recycle water, minimizing consumption and wastewater generation.
4. Versatility and Adaptability
Heat exchangers come in various designs (shell-and-tube, plate, air-cooled, etc.), making them suitable for diverse applications.
- Wide Range of Applications: Used in heating, cooling, condensation, evaporation, and heat recovery across multiple industries.
- Compact and Modular Designs: Plate heat exchangers, for example, offer high efficiency in a small footprint, ideal for space-constrained facilities.
- Compatibility with Different Fluids: Heat exchangers can handle gases, liquids, and even multiphase flows, making them adaptable to various industrial needs.
5. Extended Equipment Lifespan
By optimizing thermal management, heat exchangers reduce wear and tear on industrial machinery.
- Prevents Overheating: Excessive heat can damage equipment, but heat exchangers help maintain safe operating temperatures.
- Reduces Thermal Stress: Consistent temperature control minimizes expansion and contraction stresses in pipes and reactors.
- Corrosion Resistance: Advanced materials (stainless steel, titanium, alloys) in heat exchangers resist corrosion, ensuring long-term durability.
6. Improved Product Quality
In industries like food processing and pharmaceuticals, precise temperature control is essential for product integrity.
- Prevents Degradation: Heat exchangers ensure gentle heating or cooling, preserving the quality of heat-sensitive products (e.g., milk, vaccines, chemicals).
- Consistent Output: Uniform thermal processing leads to higher-quality end products with fewer defects.
7. Reduced Maintenance and Operational Downtime
Modern heat exchangers are designed for easy maintenance and reliability.
- Self-Cleaning Options: Some designs (like spiral or scraped-surface heat exchangers) minimize fouling, reducing cleaning frequency.
- Easy Inspection and Repair: Modular designs allow for quick disassembly and maintenance without shutting down entire processes.
- Long Service Life: High-quality materials and efficient designs ensure minimal breakdowns and extended operational life.
Applications of Heat Exchangers in Various Industries
Heat exchangers are indispensable components in modern industrial processes, enabling efficient heat transfer between fluids while maintaining separation. Their applications span across numerous industries, each with unique requirements and operational challenges. Below is an expanded look at how different sectors utilize heat exchangers to enhance efficiency, safety, and productivity.
1. Oil & Gas Industry
Crude Oil Refining
Heat exchangers preheat crude oil before it enters distillation columns, significantly improving the separation efficiency of hydrocarbons. By recovering heat from process streams, they reduce the energy required for heating, lowering operational costs. Shell-and-tube heat exchangers are commonly used due to their ability to handle high temperatures and pressures.
Natural Gas Processing
In gas processing plants, heat exchangers cool natural gas to remove impurities like water vapor and hydrocarbons. They also facilitate condensation processes in dew point control units. Plate-fin and brazed plate heat exchangers are preferred for their compact design and high thermal efficiency in cryogenic applications.
LNG (Liquefied Natural Gas) Plants
Heat exchangers play a critical role in liquefaction, where natural gas is cooled to -162°C for storage and transport. They are also used in regasification terminals to convert LNG back into gaseous form. Spiral-wound and printed circuit heat exchangers (PCHEs) are commonly employed for their superior performance in extreme temperature conditions.
2. Chemical & Petrochemical Industry
Reactor Cooling
Exothermic chemical reactions generate significant heat, which must be removed to maintain optimal reaction conditions and prevent thermal runaway. Heat exchangers circulate cooling fluids to regulate reactor temperatures, ensuring product consistency and safety.
Distillation Columns
Heat exchangers provide the necessary heating and cooling for distillation processes, separating chemical compounds based on boiling points. Reboilers heat the bottom product, while condensers cool the overhead vapors, improving separation efficiency.
Solvent Recovery
In processes involving volatile solvents, heat exchangers recover heat from vaporized solvents, condensing them for reuse. This not only reduces raw material costs but also minimizes environmental emissions.
3. Power Generation
Steam Condensers
In thermal power plants, condensers convert exhaust steam from turbines back into water, creating a vacuum that improves turbine efficiency. Surface condensers, typically shell-and-tube designs, are widely used for their reliability and high heat transfer rates.
Nuclear Power Plants
Heat exchangers transfer heat from nuclear reactors to secondary loops, generating steam to drive turbines. They also play a role in emergency cooling systems to prevent overheating during shutdowns.
Waste Heat Recovery
Industrial power plants use heat exchangers to capture waste heat from exhaust gases or cooling systems. This recovered energy can preheat feedwater or supply district heating, significantly improving overall plant efficiency.
4. Food & Beverage Industry
Pasteurization
Heat exchangers rapidly heat and cool liquids like milk and juice to kill pathogens without compromising taste or nutritional value. Plate heat exchangers are favored for their sanitary design and ease of cleaning.
Sterilization
Ultra-high-temperature (UHT) processing relies on heat exchangers to sterilize products before packaging. This extends shelf life while maintaining food safety standards.
Chilling & Freezing
Heat exchangers quickly cool products like ice cream and ready-to-eat meals, preserving texture and flavor. Scraped-surface heat exchangers prevent fouling during freezing processes.
5. HVAC & Refrigeration
Air Conditioning Systems
Heat exchangers in AC units (condensers and evaporators) transfer heat between refrigerant and air, regulating indoor temperatures. Compact designs like microchannel heat exchangers improve energy efficiency.
Heat Pumps
Heat pumps use heat exchangers to extract thermal energy from air, water, or ground sources for heating buildings. Reversible systems can also provide cooling, making them versatile for year-round use.
District Heating
Large-scale heat exchangers distribute hot water from centralized plants to residential and commercial buildings, reducing individual energy consumption.
6. Pharmaceutical Industry
Vaccine Production
Precise temperature control is critical in vaccine manufacturing. Heat exchangers maintain strict thermal conditions during fermentation, purification, and storage.
API (Active Pharmaceutical Ingredient) Processing
Heat exchangers regulate temperatures in chemical synthesis, crystallization, and drying processes, ensuring consistent product quality.
Sterile Filling
In aseptic packaging lines, heat exchangers sterilize containers and closures using superheated steam or hot air, preventing contamination.
7. Automotive & Aerospace
Engine Cooling
Radiators (a type of heat exchanger) dissipate heat from engine coolant, preventing overheating. Advanced materials like aluminum improve thermal conductivity and weight savings.
Exhaust Gas Recirculation (EGR)
EGR systems use heat exchangers to cool exhaust gases before reintroducing them into the engine, reducing nitrogen oxide (NOx) emissions.
Aircraft Climate Control
Air-to-air heat exchangers regulate cabin temperatures while managing engine and avionics cooling needs.
8. Marine Industry
Seawater Cooling
Heat exchangers use seawater to cool ship engines and auxiliary systems, preventing overheating in harsh marine environments.
Desalination Plants
Multi-stage flash (MSF) and reverse osmosis (RO) desalination systems rely on heat exchangers for energy-efficient freshwater production.
LNG Carriers
Specialized heat exchangers maintain cryogenic temperatures during LNG transport, ensuring safe and efficient fuel delivery.
9. Renewable Energy Systems
Solar Thermal Plants
Heat exchangers transfer heat from solar collectors to working fluids, generating steam to drive turbines in concentrated solar power (CSP) plants.
Geothermal Energy
Heat exchangers extract heat from underground sources, transferring it to power plants or direct heating systems.
Biogas Plants
Anaerobic digesters use heat exchangers to maintain optimal temperatures for microbial activity, maximizing biogas production.
Conclusion
From energy-intensive oil refineries to precision-driven pharmaceutical labs, heat exchangers are vital for optimizing processes, reducing costs, and enhancing sustainability. Their adaptability to diverse operational needs underscores their importance in modern industry.